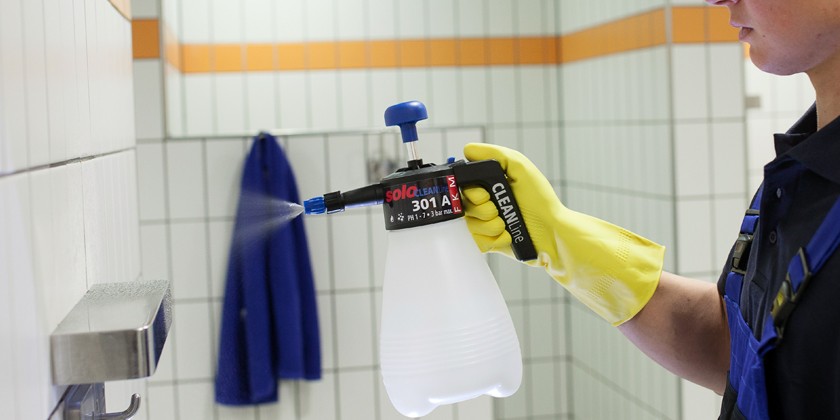
For the past half century, people have been using inexpensive trigger sprayers for many types of facility management chemical applications. Whether for disinfecting hard surfaces in health care applications, or for cleaning and degreasing in industrial environments, basic trigger sprayers are helpful for dispersing chemicals into targeted areas.
Although hand-operated trigger sprayers can get the job done, they are inefficient and outdated. Hand fatigue is a common problem, and manual trigger-style sprayers can only cover limited surface areas at a time. Pressure applicators are easier to use and allow users to cover more surface area in less time.
REDUCE FATIGUE:
Using a pressure instead of a trigger sprayer will enable the user to do his job more efficiently, while eliminating the hand fatigue and repetitive use injury problems commonly experienced with trigger sprayers. This equates to happier workers and increased productivity. The correct pressure sprayer will allow you to get maximum performance from your employees.
PROPER CHEMICAL MIXING:
Proper chemical mixing can also be a challenge when using trigger sprayers. Trying to dilute industrial chemicals into small openings can result in incorrect dilution and spillage. As a consequence, you may have wasted product, a chemical ratio that is too strong or too mild for the job, or worse dangerous chemical spills on people and on surfaces. Less waste = lower chemical costs, improving facility management profitability.
CHOOSING THE RIGHT SPRAYER FOR THE JOB:
Choosing the right chemical applicator depends on the particular application and the chemicals required to produce the desired results. With the new range of chemical applicators currently available, there is a sprayer to fit any spraying job.
POPULAR FACILITIES MAINTENANCE SPRAYER TYPES INCLUDE:
- High Acid Sprayers (pH 1-7) – Sprayers with FKM (Viton) seals are best for the highly acidic chemicals used in sanitary cleaning solutions. These sprayers can also be used with solutions that contain oil and solvents. Sealed pump systems prevent aggressive liquids from causing internal mechanical damage, leading to a long service life.
- General Use Sprayers (pH 7-14) – Sprayers with EPDM seals are best for alkaline solutions, such as sprayers used for degreasing fat and oil, cleaning glass and disinfecting surfaces. Quality nozzles ensure an even and direct spray pattern of the solution.
- Foam Sprayers – Foam sprayers are available with FKM (Viton) seals (high acid) or EPDM (alkaline) seals for low moisture solutions. An adjustable nozzle allows the user to control the spray, ensuring a fast and even application, while minimizing run off.
OTHER FEATURES TO CONSIDER:
- Choose the right size tank for the widest range of use. Tanks typically range from 1 liter – 4 gallons.
- Ensure the pumps are sturdy and provide effortless build up.
- Parts made from non-corrosive materials ensure a long life.
- Ergonomically shaped designs are easier for employees to handle.
To gain the longest life from your pressure sprayer make sure to rinse it thoroughly after each use!
Improve your facility management operations! With the value of pressurized sprayers versus the affordable price point, it just makes sense to upgrade to a pressure chemical sprayer.
For information on Solo CleanLine sprayers visit our website at www.solousa.com